I'm experimenting with simple circuits to generate square waves, for use as inputs and clock sources for use in more complex circuits.
I tried the "50% Duty Cycle Astable Oscillator" based on a 555 timer from this site:
http://www.electronics-tutorials.ws/waveforms/555_oscillator.html
Here's the schematic, from the above web page:
I built it and it works, but I'm getting a large amount of overshoot on the rising edge of the square wave and would like to clean it up.
Here's a scope trace, showing the problem. The yellow trace is the output (pin 3) and the blue trace is the threshold (pin 6), representing the charge stored in C1.
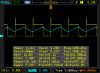
Here's a closer look at the rising edge: The vertical white line is the point in time when the capacitor (C1) stops discharging and begins charging again.
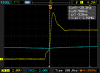
I'm using a Vcc voltage of 9V (from six AA alkaline batteries) and the peak on this overshoot is 12V.
Because it exceeds the voltage of the batteries, my first thought was that it might be parasitic inductance or voltage fluctuations from the batteries. (I haven't tried a well-regulated power supply.)
So, I put a large electrolytic capacitor across GND to Vcc to even out the voltage.
That reduced the magnitude of the overshoot, but prolonged the duration:
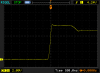
Do you know what might be causing the 350-400ns 1V overshoot on the waveform above?
Given the stable and non-oscillating shape of the overshoot, I suspect it's a 'feature' of the 555 circuit shown at the beginning of this post.
---Xeno
I tried the "50% Duty Cycle Astable Oscillator" based on a 555 timer from this site:
http://www.electronics-tutorials.ws/waveforms/555_oscillator.html
Here's the schematic, from the above web page:

I built it and it works, but I'm getting a large amount of overshoot on the rising edge of the square wave and would like to clean it up.
Here's a scope trace, showing the problem. The yellow trace is the output (pin 3) and the blue trace is the threshold (pin 6), representing the charge stored in C1.
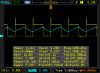
Here's a closer look at the rising edge: The vertical white line is the point in time when the capacitor (C1) stops discharging and begins charging again.
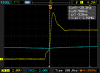
I'm using a Vcc voltage of 9V (from six AA alkaline batteries) and the peak on this overshoot is 12V.
Because it exceeds the voltage of the batteries, my first thought was that it might be parasitic inductance or voltage fluctuations from the batteries. (I haven't tried a well-regulated power supply.)
So, I put a large electrolytic capacitor across GND to Vcc to even out the voltage.
That reduced the magnitude of the overshoot, but prolonged the duration:
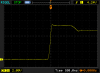
Do you know what might be causing the 350-400ns 1V overshoot on the waveform above?
Given the stable and non-oscillating shape of the overshoot, I suspect it's a 'feature' of the 555 circuit shown at the beginning of this post.
---Xeno