Dear all,
I have a very strange problem.
I have the following circuit (picture attached):
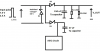
The circuit receives discrete pulses with 7.5 V amplitude and 2.5 A of current over 1-2 ms. The voltage is then stabilzed by a zener voltage at around 5.6 V. Then the capacitor of 150 uF will store the energy and keep the voltage at a quasi-stable state during long time (over seconds...). This capacitor is a SMD tantalum capacitor.
There is also an Asic circuit (with quartz, reset circuit etc.) but they are not of interest in my problem!
My problem:
For some reasons, we should put this circuit in a device generating a high mechancial force (without damaging the circuit). So the circuit is under very high force (something like high air pressure) for a few seconds.
After this test,we recover the circuit. We understood that after the test, our 150 uF capacitor fails to store the energy. So it discharges very rapidly. We checked the capacitor and it is not broken.
My questions:
Could you please tell me that in this case:
1. Is there any problem with the circuit itself (without considering the mechanical test)?
2. Is it the mechanical test which can cause the circuit to fail?
4. What can happen inside this kind of capacitor to fail?
Thank you very much for your help and bests regards.
l. Ram
I have a very strange problem.
I have the following circuit (picture attached):
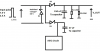
The circuit receives discrete pulses with 7.5 V amplitude and 2.5 A of current over 1-2 ms. The voltage is then stabilzed by a zener voltage at around 5.6 V. Then the capacitor of 150 uF will store the energy and keep the voltage at a quasi-stable state during long time (over seconds...). This capacitor is a SMD tantalum capacitor.
There is also an Asic circuit (with quartz, reset circuit etc.) but they are not of interest in my problem!
My problem:
For some reasons, we should put this circuit in a device generating a high mechancial force (without damaging the circuit). So the circuit is under very high force (something like high air pressure) for a few seconds.
After this test,we recover the circuit. We understood that after the test, our 150 uF capacitor fails to store the energy. So it discharges very rapidly. We checked the capacitor and it is not broken.
My questions:
Could you please tell me that in this case:
1. Is there any problem with the circuit itself (without considering the mechanical test)?
2. Is it the mechanical test which can cause the circuit to fail?
4. What can happen inside this kind of capacitor to fail?
Thank you very much for your help and bests regards.
l. Ram
Attachments
Last edited: