Hello, Everyone! My name is Nicholas Salay, and this is actually my first post on the forums. I'm hoping I can eventually add more to the community than I ask, but at the moment, I'm a bit green, fresh out of college. I'm writing today because, as the name suggests, I'm trying to limit the RPM of a Milwaukee drill from 0-850 RPM to about 0-475 RPM (Actually any maximum RPM within a range of 450-500 RPM is okay here). I can also accept power inefficiencies - that's fine. This drill is corded and works off of a 120Vrms 60Hz wall outlet.
This is not a single drill I am modifying, but rather a large line of drills that are continuously being ordered for the company I work for. So I need a solution that is not only relatively cheap, but also not very labor intensive to install.
The drill in question that I am modifying can be found here:
https://www.toolbarn.com/milwaukee-0299-20.html
This is a single-phase AC induction motor, running at 8A.
Now my traditional approach to controlling an AC motor like this has always been to use a basic triac circuit, something like the following:
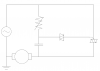
However, the drill already has a similar circuit to this (though it uses an SCR rather than a triac).
For those interested in the circuit in the drill itself, the only information I have is from actually disassembling the thing, unfortunately.
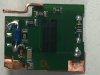
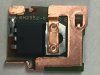
That SCR is a TYN616. I've attached the relevant datasheet.
There is a conductive brush connected to the trigger of the drill, which touches those carbon film strips on the board. This is the potentiometer of the circuit.
The easy thing to do would be to modify this circuit and replace one of those resistors with a larger value until I get the RPM range I want, but as I recall, the housing for the switch and the motor driving circuit was sealed and I was forced to break it just to get access to this board. I've ordered a replacement switch so I can try again, but at this point, I am working under the assumption that I am unable to modify this board and still expect the entire motor driving mechanism to be in appropriate condition for company use.
The current solution I'm investigating for this problem is to have my own motor driving circuit in parallel with this one, which would specifically be tuned to very specific RPM for the drill, 475 RPM, and has no capabilities to vary that setting. Both my and Milwaukee's motor control circuits would be inputs towards a selector circuit, which compares both signals and passes only the signal with the lowest power to the drill (or the signal that is clipping the most of the AC source). However, I don't know how I would make such a circuit.
So, first of all, am I even taking the right approach here? If so, how would I be able to select the lowest power waveform from the motor driving circuits I described? If not, what should I be doing instead?
I will try to answer your questions to the best of my ability, but I have already given most of the information I have on the subject.
Thank you very much for your consideration into my problem. Hopefully, the solution is something very simple that I am just missing.
This is not a single drill I am modifying, but rather a large line of drills that are continuously being ordered for the company I work for. So I need a solution that is not only relatively cheap, but also not very labor intensive to install.
The drill in question that I am modifying can be found here:
https://www.toolbarn.com/milwaukee-0299-20.html
This is a single-phase AC induction motor, running at 8A.
Now my traditional approach to controlling an AC motor like this has always been to use a basic triac circuit, something like the following:
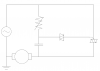
However, the drill already has a similar circuit to this (though it uses an SCR rather than a triac).
For those interested in the circuit in the drill itself, the only information I have is from actually disassembling the thing, unfortunately.
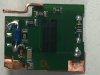
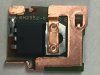
That SCR is a TYN616. I've attached the relevant datasheet.
There is a conductive brush connected to the trigger of the drill, which touches those carbon film strips on the board. This is the potentiometer of the circuit.
The easy thing to do would be to modify this circuit and replace one of those resistors with a larger value until I get the RPM range I want, but as I recall, the housing for the switch and the motor driving circuit was sealed and I was forced to break it just to get access to this board. I've ordered a replacement switch so I can try again, but at this point, I am working under the assumption that I am unable to modify this board and still expect the entire motor driving mechanism to be in appropriate condition for company use.
The current solution I'm investigating for this problem is to have my own motor driving circuit in parallel with this one, which would specifically be tuned to very specific RPM for the drill, 475 RPM, and has no capabilities to vary that setting. Both my and Milwaukee's motor control circuits would be inputs towards a selector circuit, which compares both signals and passes only the signal with the lowest power to the drill (or the signal that is clipping the most of the AC source). However, I don't know how I would make such a circuit.
So, first of all, am I even taking the right approach here? If so, how would I be able to select the lowest power waveform from the motor driving circuits I described? If not, what should I be doing instead?
I will try to answer your questions to the best of my ability, but I have already given most of the information I have on the subject.
Thank you very much for your consideration into my problem. Hopefully, the solution is something very simple that I am just missing.