may 6
continuing with discovery via experimenting w/ the U4 4047 chip that is on the 2012 CDI PCB
the exp's are taking place on a bread board for now.
goal today = show what it means for the 4047 to operate in 'gatable' mode.
.............. plus 2 circuit examples that were wired up on a bd.bd and 'scoped.
............... there are many images that result from the experimenting.
............. as well as 3 TI 4047 data pages that refer to what is going on here.
... this all is to set the stage for my eventual goal of having the 4047 emit just one pulse.
... this one-pulse-at-a-time will be for more experimenting.
first image is p.1 of the data ... to highlight the gatable feature this chip comes with
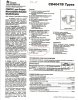
2'd image is p.2 of the data and the top-of-page table that shows us the connections to make
.................. for 'true gating' i.e. use pin 5 AST as the gating-pulse input and how we have
............... 3 pin choices where to take out gated clock output from : 10 , 11 or 13
... actually i'm not sure if pin13 , OSC, is gatable or not. it was not scoped

continuing with discovery via experimenting w/ the U4 4047 chip that is on the 2012 CDI PCB
the exp's are taking place on a bread board for now.
goal today = show what it means for the 4047 to operate in 'gatable' mode.
.............. plus 2 circuit examples that were wired up on a bd.bd and 'scoped.
............... there are many images that result from the experimenting.
............. as well as 3 TI 4047 data pages that refer to what is going on here.
... this all is to set the stage for my eventual goal of having the 4047 emit just one pulse.
... this one-pulse-at-a-time will be for more experimenting.
first image is p.1 of the data ... to highlight the gatable feature this chip comes with
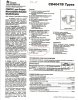
2'd image is p.2 of the data and the top-of-page table that shows us the connections to make
.................. for 'true gating' i.e. use pin 5 AST as the gating-pulse input and how we have
............... 3 pin choices where to take out gated clock output from : 10 , 11 or 13
... actually i'm not sure if pin13 , OSC, is gatable or not. it was not scoped

Last edited: