It depends on many factors. Although the frequency of the switching cycle may be only 100 kHz, there are some very rapid voltage and current changes which have large frequency components well into the tens or even hundreds of MHz. These are the one that cause the problems when inductance and capacitance are present, and when current loops are not properly controlled and kept as compact as possible. That's all I know about it.
I can't visualize where in my circuit there would exist frequencies that high running through the breadboard. Do you mean slight fluctuations in power line noise and such originating from inside the PWM chip?
Yes, as long as the diode is fast enough - something which is also true of Schottky diodes.
If you don't mind me asking, how does switching speed play a part in heat efficiency? Is there a calculation I can use incorporating switching speed to better understand how it translates to wasted heat energy? Is it anything like Complimentary MOSFETs where during the switching of one MOSFET the other will be in a shorted state for nanoseconds before it is turned on and thus generate heat?
"Voltage through" isn't meaningful. Current flows through; voltage appears across. Voltage across a diode doesn't cause it to dissipate heat, apart from rapid changes which can produce current flow through the diode's capacitance, but that's not much of a factor. Current through a diode, in the forward direction, multiplied by the diode's forward voltage, is what causes most of the power dissipation.
It's the forward voltage multiplied by the mean inductor current multiplied by the duty cycle of the diode, which is 100% minus the duty cycle of the MOSFET. You can estimate the MOSFET duty cycle under load as VOUT / VIN × 100%.
Ah, of course. I see. Thank you for that clarification.
You can't "configure" a MOSFET as a diode. If you're talking about the body diode that appears between the source and drain, this diode is just parasitic and doesn't have any impressive characteristics at all. When a MOSFET is used as a synchronous rectifier, its gate is driven by the controller IC and it is not used as a diode; it is just used to provide the path to 0V that the diode would otherwise provide. It's a lot more efficient than a diode because a MOSFET with gate bias has no equivalent of forward voltage in its drain-source path and its ON-resistance (RDS(on)) can be very low.
Would this configuration work? Note the MOSFET in place of where the diode would normally be.
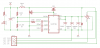
That's OK. "Input should be on the left" is the main criticism. Personally I like to show the high-current ground path explicitly in my schematics. Here's an example from a product I designed that shows what I mean. Ignore the fact that the power input is on the right! There were reasons for this; I'm not sure whether I still think they justify drawing it backwards or not!
View attachment 18922
I like this strategy a lot. I've been using a freehand paint program to draw the schematics presented in this thread based on an original screenshot of my Eagle CAD project. I'll check to see if Eagle has a feature to visually indicate high amp traces on the schematic sheets for my production version.