Hey all, first post and new to most of this stuff as I am more of an automotive fabricator. I need to build something for shifting a sequential transmission forward and reverse electronically. I have an old electric push button shifter (see below) that has for some reason stopped working, but I’m trying to fix it if possible.
This uses a motor and a lead screw to create the linear motion, but it really is quite old technology. As you can see, there are micro switches that presumably reverse the polarity to return it to the middle after shifting. All this happens in about 50ms. The shaft is also broken, but because the motor no longer spins I am unable to pull it apart to see what type of motor they used. It is very powerful as well, probably 20 pounds of force if I was guessing. Only two wires going to the motor.
With today’s stepper motors and servo motors, what would be the fastest way of doing this? It would be nice if it could be cut down to around 20ms per shift. I have access to mills, lathes, and welding so I can definitely build whatever to make it work. The new version of this product is rotary based, though the time is still the same, and they are quite expensive. Plus I’m more of a diy guy anyway.
Any help would be greatly appreciated!!
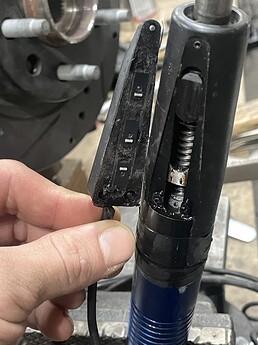
This uses a motor and a lead screw to create the linear motion, but it really is quite old technology. As you can see, there are micro switches that presumably reverse the polarity to return it to the middle after shifting. All this happens in about 50ms. The shaft is also broken, but because the motor no longer spins I am unable to pull it apart to see what type of motor they used. It is very powerful as well, probably 20 pounds of force if I was guessing. Only two wires going to the motor.
With today’s stepper motors and servo motors, what would be the fastest way of doing this? It would be nice if it could be cut down to around 20ms per shift. I have access to mills, lathes, and welding so I can definitely build whatever to make it work. The new version of this product is rotary based, though the time is still the same, and they are quite expensive. Plus I’m more of a diy guy anyway.
Any help would be greatly appreciated!!