I want to charge a bank of 12 v deep cycles with that cheesy harbor freight generator have.
Thats what made me think of it,
My idea for maximum efficiency was to get a variac , used to have one but and connect it to an old school battery charger (with non of that automatic nonsense) on boost-start then I could push the 700 w generator to its maximum to reduce the time I have to listen to that noise.
Am I missing anything ?

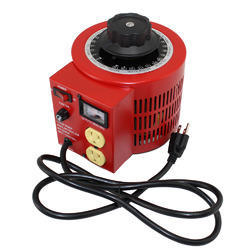
how can this be increased in order to speed up charging time?
Thanks.
Thats what made me think of it,
My idea for maximum efficiency was to get a variac , used to have one but and connect it to an old school battery charger (with non of that automatic nonsense) on boost-start then I could push the 700 w generator to its maximum to reduce the time I have to listen to that noise.
Am I missing anything ?