I want to do some experimentation with a 60v charger connected to 17x Lifepo4 cells in series.
The idea is the 2 resistor voltage divider will be connected across Battery Bank.
The voltage between resistors is Bank Voltage divided by number of cells.
Shown are (16KΩ + 1KΩ) resistor values for 17 cell Bank
So the voltage between resistors is the equivalent of a single cells charge voltage.
The 1 17th voltage will follow voltage changes across the bank.
What would be the best IC or circuit for at least 1/1.5 Amp output.
The idea is the 2 resistor voltage divider will be connected across Battery Bank.
The voltage between resistors is Bank Voltage divided by number of cells.
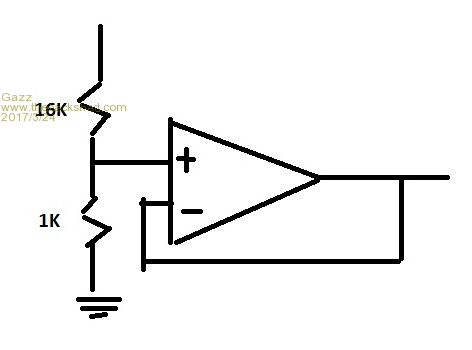
Shown are (16KΩ + 1KΩ) resistor values for 17 cell Bank
So the voltage between resistors is the equivalent of a single cells charge voltage.
The 1 17th voltage will follow voltage changes across the bank.
What would be the best IC or circuit for at least 1/1.5 Amp output.