Hi.
I have salvaged a 12 VDC motor from an old tyre-inflation compressor pump.
My plan is to replace the weak 3 VDC motor in my portable, rechargeable mini-vac for car with this 12 V motor, which can then plug directly into the cigar-lighter via the DC socket & 'run' switch.
Both motors are identical dimensions, physically, except that old vac motor has no gear on the shaft, and old compressor motor does, which drove the cam via a secondary step-down gear.
The gear needs to come off, to allow the plastic fan to be pushed onto bare shaft.
Problem - I can't figure out how it comes off!
Tried pulling, levering, heating with a heat-gun to 'expand' it if press-fitted.
Even cut the gear in two, halfway along its length, thinking that a shorter piece may be easier to pull off. (Spun motor on 12 V while holding junior hacksaw then triangular file to cut & groove it).
Nothing doing.
As a last resort, if all else fails, would ferric chloride eat through the shaft?
(Suspect it is stainless steel).
I'm wary of 'etching' the gear away with Ferric Chloride, as if the solution 'wicks' into the motor's front-end bush, it may destroy the bush, especially if it is copper/brass material.
Alternatively, I'll spin the motor up again, this time using a flat file to 'lathe' the brass gear to shaft level.
Thanks, Clive.
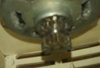
I have salvaged a 12 VDC motor from an old tyre-inflation compressor pump.
My plan is to replace the weak 3 VDC motor in my portable, rechargeable mini-vac for car with this 12 V motor, which can then plug directly into the cigar-lighter via the DC socket & 'run' switch.
Both motors are identical dimensions, physically, except that old vac motor has no gear on the shaft, and old compressor motor does, which drove the cam via a secondary step-down gear.
The gear needs to come off, to allow the plastic fan to be pushed onto bare shaft.
Problem - I can't figure out how it comes off!
Tried pulling, levering, heating with a heat-gun to 'expand' it if press-fitted.
Even cut the gear in two, halfway along its length, thinking that a shorter piece may be easier to pull off. (Spun motor on 12 V while holding junior hacksaw then triangular file to cut & groove it).
Nothing doing.
As a last resort, if all else fails, would ferric chloride eat through the shaft?
(Suspect it is stainless steel).
I'm wary of 'etching' the gear away with Ferric Chloride, as if the solution 'wicks' into the motor's front-end bush, it may destroy the bush, especially if it is copper/brass material.
Alternatively, I'll spin the motor up again, this time using a flat file to 'lathe' the brass gear to shaft level.
Thanks, Clive.
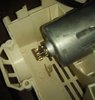
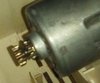
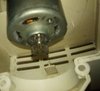
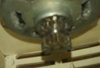
Last edited: