( Behold . . . . my first and ever . . . CREATED . . . post. )
Sires . . . . . . . for your evaluation and comments:
Speedy PCB production using an inkjet printer
Rapid PCB production for prototype circuits is an old theme. A copper-clad board with a photosensitive mask and an etching bath of caustic chemicals is messy, time-consuming and really yesterday’s technology.
Use a specialist PCB production facility and you’re looking at a few days turnaround time, a milling machine will do the job quicker but you need the equipment to start off with. 3D printing conductive tracks has been achieved but the technology is still not main-stream. How about 2D printing direct from an ink-jet printer?
Well the answer to that one is yes! PHD student Varun Perumal Chadalavada at the University of Toronto has developed an amazingly simple technique which can be used with commercial inkjet printers to ‘print’ a prototype PCB. It has been likened to the instant ‘Polaroid’ land film process where an image is impressed on a complex chemical layer and you need to wait a while until the image appears.
The technique prints the PCB pattern onto a sheet of Printem film which is then exposed to light for around 30 seconds and then the top layer is peeled back to reveal the PCB, that’s it!
The processing speed is just about unbeatable. It would be ideal for any lab or workshop when you just want to knock up a quick prototype.
A spin-off company has been formed in order to explore the potential market for the product. Technical specs such as track thickness, stability of the product, its durability and solderability and production costs are not yet finalized but from the video above, the process looks very promising.
Watch this . . .
Now I can see the intertransfer between the two layers of "film" more readily, if related to laser "heat" was involved, by the utilization of a Laser printer.
BUT, in the use of inkjet technology . . .would the mention of a custom ink . . .read as liquid CHEMICAL . . . have been left out.
And then, the transfer, via intra layer mode, be related to a wetting of the top layer and then "weep" transferrance . . . . . and just how defined could that lateral transferrance "creep" be controlled to.
Notice the high mil width traces being shown, along with some dots of drill thru hole markings being non transferred.
This ALONG with the resultant / apparent deposited foils density / thickness. ( 'Ya ever do any gold leaf work ?)
Soldering ?. . . . .suspecting the use of a 15 watt iron and the most flux activated and fine diameter wire solder available, along with a 3 second on board soldering time.
FORGET the use of a lead free solder . . . .which I have considered, NOT using, for yet another 50 years.
Personally . . . . . methinks . . . . . that they are BLOWING the whistles, BANGING the drums and SHOUTING
. . . .W A A A A A A Y too early in its technological development curve.
HOWEVER in the looking up of that video URL addee . . . .I am additionally finding this . . .more promising . . .
And of course, isn't this being the end degree of perfection that you REALLY-REALLY want.
5 Minutes in milling that board and 5 minutes in "stuffing " it !
( AND 5 hours in its layout, artwork and path debugging ! )
73's de Edd
Sires . . . . . . . for your evaluation and comments:
Speedy PCB production using an inkjet printer
Rapid PCB production for prototype circuits is an old theme. A copper-clad board with a photosensitive mask and an etching bath of caustic chemicals is messy, time-consuming and really yesterday’s technology.
Use a specialist PCB production facility and you’re looking at a few days turnaround time, a milling machine will do the job quicker but you need the equipment to start off with. 3D printing conductive tracks has been achieved but the technology is still not main-stream. How about 2D printing direct from an ink-jet printer?
Well the answer to that one is yes! PHD student Varun Perumal Chadalavada at the University of Toronto has developed an amazingly simple technique which can be used with commercial inkjet printers to ‘print’ a prototype PCB. It has been likened to the instant ‘Polaroid’ land film process where an image is impressed on a complex chemical layer and you need to wait a while until the image appears.
The technique prints the PCB pattern onto a sheet of Printem film which is then exposed to light for around 30 seconds and then the top layer is peeled back to reveal the PCB, that’s it!
The processing speed is just about unbeatable. It would be ideal for any lab or workshop when you just want to knock up a quick prototype.
A spin-off company has been formed in order to explore the potential market for the product. Technical specs such as track thickness, stability of the product, its durability and solderability and production costs are not yet finalized but from the video above, the process looks very promising.
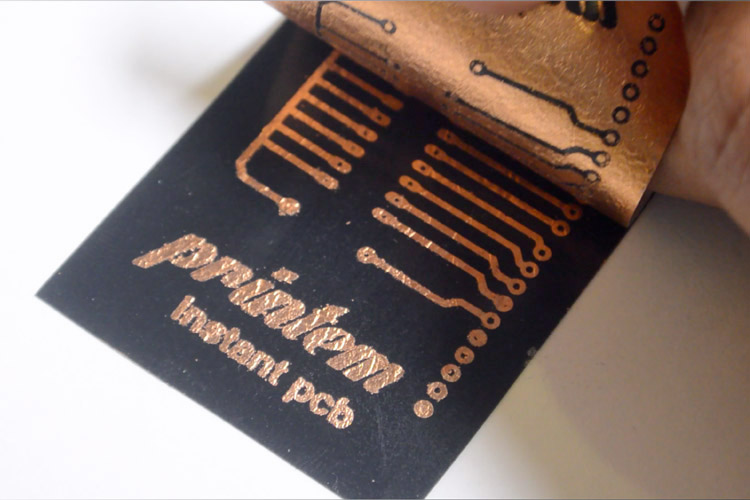
Watch this . . .
Now I can see the intertransfer between the two layers of "film" more readily, if related to laser "heat" was involved, by the utilization of a Laser printer.
BUT, in the use of inkjet technology . . .would the mention of a custom ink . . .read as liquid CHEMICAL . . . have been left out.
And then, the transfer, via intra layer mode, be related to a wetting of the top layer and then "weep" transferrance . . . . . and just how defined could that lateral transferrance "creep" be controlled to.
Notice the high mil width traces being shown, along with some dots of drill thru hole markings being non transferred.
This ALONG with the resultant / apparent deposited foils density / thickness. ( 'Ya ever do any gold leaf work ?)
Soldering ?. . . . .suspecting the use of a 15 watt iron and the most flux activated and fine diameter wire solder available, along with a 3 second on board soldering time.
FORGET the use of a lead free solder . . . .which I have considered, NOT using, for yet another 50 years.
Personally . . . . . methinks . . . . . that they are BLOWING the whistles, BANGING the drums and SHOUTING
. . . .W A A A A A A Y too early in its technological development curve.
HOWEVER in the looking up of that video URL addee . . . .I am additionally finding this . . .more promising . . .
And of course, isn't this being the end degree of perfection that you REALLY-REALLY want.
5 Minutes in milling that board and 5 minutes in "stuffing " it !
( AND 5 hours in its layout, artwork and path debugging ! )
73's de Edd
Last edited by a moderator: