Hi, I'm new here.
We have an oven with a shaded pole AC fan motor - 120VAC, 40W, 3K rpm (the inserted photo is very similar). Since the oven manufacturer cheaped out big time, the plastic fan wobbles badly, generating a very loud vibration noise. I'd like to slow the fan down. I figure that 50-75% speed will eliminate the noise while still providing the cooling the oven requires. I tried a ceiling fan speed control, presumably triac based, but it works too well, slowing down to about 25% speed. While messing with that, I discovered that the fan slows way down when my bench vise jaws clasp the magnetized stator. Further experimentation revealed that any sizable ferrous metal also slows it down. I'm sure I can find just the right size to bring the rpm down to the range I want.
My question is: Will the shaded pole motor be happy with this chunk of metal attached, or will it overheat or otherwise fail?
Thanks in advance,
Tenaya
We have an oven with a shaded pole AC fan motor - 120VAC, 40W, 3K rpm (the inserted photo is very similar). Since the oven manufacturer cheaped out big time, the plastic fan wobbles badly, generating a very loud vibration noise. I'd like to slow the fan down. I figure that 50-75% speed will eliminate the noise while still providing the cooling the oven requires. I tried a ceiling fan speed control, presumably triac based, but it works too well, slowing down to about 25% speed. While messing with that, I discovered that the fan slows way down when my bench vise jaws clasp the magnetized stator. Further experimentation revealed that any sizable ferrous metal also slows it down. I'm sure I can find just the right size to bring the rpm down to the range I want.
My question is: Will the shaded pole motor be happy with this chunk of metal attached, or will it overheat or otherwise fail?
Thanks in advance,
Tenaya
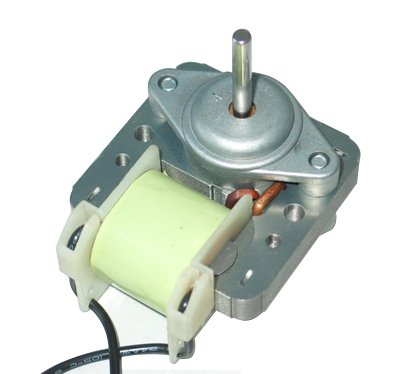