Hi all,
I'm a software guy who wishes he knew more about hardware and have played with circuits some but am very frequently stumped or find myself saying "I don't know how this is possible, but this is indeed happening" which can get pretty frustrating.
So here's my latest thing:
I have a circuit in my 33 year old car that is getting very hot and I'm afraid will start a fire. It's the connection to the 450W radiator fan. At 12V, it seems like it should be carrying 37.5A, but the correct fuse, per the manual and everyone online, is 16A, which itself doesn't make any sense (comments welcome).
My actual question however was I'm thinking the age of the wires + the crusty and slightly burned GBC fuse holder are causing increased resistance. I was thinking this would cause higher current but as I write this I realize in theory the higher resistance should lower the current. Regardless, it's getting hot, so I wanted to measure the resistance of the components in the circuit. I measured parts of the circuit and then had (what I thought was) a bright idea to just measure the resistance from the battery to the fan, expecting it to be high. I thought I would then clean parts and replace old connectors, re-measure and see a lower resistance. I needed a length of wire so I measured its resistance first. Below is what I saw and why I am confused.
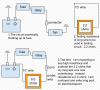
I'm a software guy who wishes he knew more about hardware and have played with circuits some but am very frequently stumped or find myself saying "I don't know how this is possible, but this is indeed happening" which can get pretty frustrating.
So here's my latest thing:
I have a circuit in my 33 year old car that is getting very hot and I'm afraid will start a fire. It's the connection to the 450W radiator fan. At 12V, it seems like it should be carrying 37.5A, but the correct fuse, per the manual and everyone online, is 16A, which itself doesn't make any sense (comments welcome).
My actual question however was I'm thinking the age of the wires + the crusty and slightly burned GBC fuse holder are causing increased resistance. I was thinking this would cause higher current but as I write this I realize in theory the higher resistance should lower the current. Regardless, it's getting hot, so I wanted to measure the resistance of the components in the circuit. I measured parts of the circuit and then had (what I thought was) a bright idea to just measure the resistance from the battery to the fan, expecting it to be high. I thought I would then clean parts and replace old connectors, re-measure and see a lower resistance. I needed a length of wire so I measured its resistance first. Below is what I saw and why I am confused.
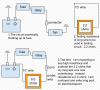