Hi guys I had a previous thread helping me wire up a 5v relay to a toggle switch and a cap to make flicking the toggle switch pulse the relay turning the toggle switch into a momentary switch.
Once I got that circuit done I went ahead and bought a bank of 8 5V relays on a board to make it easier for me to wire up 8 switches to do this, however it has just confused me more!!
The previous wiring diagrams I followed to create the momentary switch are below:
Now when I have come to wire this up on this relay board I have a couple of issues, one is that I now need a GND, VCC and IN1 from the relay going to my breadboard and that confused me as before I only had two wires so that threw me off.
Second I am not sure if my capacitor is the wrong size for this bank because they have transistors already in there etc?
Here is what I have and I will explain what happens when I throw the switch!
5V 1.0A USB Power
16v 220uf Capacitor
8 Channel 5V Relay Panel:
SPEC: http://www.ebay.co.uk/itm/262346134998?_trksid=p2057872.m2749.l2648&ssPageName=STRK:MEBIDX:IT
So when I toggle the switch the relay clicks, the LED on the relay comes on and then after a second the relay clicks back and the LED is pretty much out but still dimming over time. Now that is what i want! Maybe I want it to only be on for a split second rather than a full second but that's not my real issue. The issue then is if I toggle the switch the other way I want it to do the same thing cause the relay to click on and then back. Instead I get no response, and then toggling it back the other way which worked before will only work if I give it say 5-10 seconds break in the non working position, I am guessing to let the cap charge or something??
I am in a little over my head and would really appreciate some help! I just want the toggle switch to throw the relay on and then off every toggle back and forth, without having to wait for the cap / whatever it is to charge!
Can someone take a look at my wiring, have I put something in the wrong place? Is the cap I am using the wrong spec?
Thanks in advance guys and I appreciate the help thus far!
Once I got that circuit done I went ahead and bought a bank of 8 5V relays on a board to make it easier for me to wire up 8 switches to do this, however it has just confused me more!!
The previous wiring diagrams I followed to create the momentary switch are below:
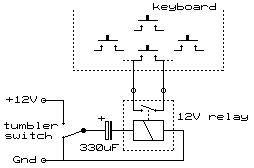

Now when I have come to wire this up on this relay board I have a couple of issues, one is that I now need a GND, VCC and IN1 from the relay going to my breadboard and that confused me as before I only had two wires so that threw me off.
Second I am not sure if my capacitor is the wrong size for this bank because they have transistors already in there etc?
Here is what I have and I will explain what happens when I throw the switch!
5V 1.0A USB Power
16v 220uf Capacitor
8 Channel 5V Relay Panel:
SPEC: http://www.ebay.co.uk/itm/262346134998?_trksid=p2057872.m2749.l2648&ssPageName=STRK:MEBIDX:IT

So when I toggle the switch the relay clicks, the LED on the relay comes on and then after a second the relay clicks back and the LED is pretty much out but still dimming over time. Now that is what i want! Maybe I want it to only be on for a split second rather than a full second but that's not my real issue. The issue then is if I toggle the switch the other way I want it to do the same thing cause the relay to click on and then back. Instead I get no response, and then toggling it back the other way which worked before will only work if I give it say 5-10 seconds break in the non working position, I am guessing to let the cap charge or something??
I am in a little over my head and would really appreciate some help! I just want the toggle switch to throw the relay on and then off every toggle back and forth, without having to wait for the cap / whatever it is to charge!
Can someone take a look at my wiring, have I put something in the wrong place? Is the cap I am using the wrong spec?
Thanks in advance guys and I appreciate the help thus far!