hello my friends
i am trying to build a linear analog servo drive for a servo motor and YES it is analog not a PWM for many reasons one of them :is that this drive is a part of control system i am working on and i want to reduce the noise to minimum.
so i dig the web and i found several power op amp: like L165,L2720, LM675,LM12
i am kid of confused because all i want is :
Class-AB linear power Amplifier with no distortion around zero
i am trying to use the power op-amp rather than power transistors to reduce the number of components and the issues related to them .
here is the motor specifications:
http://www.specamotor.com/en/Faulhaber/motors/2338-006S/datasheet_motor.html
i suppose to control the position in bi-direction.
the questions:
1-which power op-amp should i use?
2- is there a ready drive that i can buy ?
3-is this circuit correct to control the motor position in bi-direction?
any help will be more than appreciated
i am trying to build a linear analog servo drive for a servo motor and YES it is analog not a PWM for many reasons one of them :is that this drive is a part of control system i am working on and i want to reduce the noise to minimum.
so i dig the web and i found several power op amp: like L165,L2720, LM675,LM12
i am kid of confused because all i want is :
Class-AB linear power Amplifier with no distortion around zero
i am trying to use the power op-amp rather than power transistors to reduce the number of components and the issues related to them .
here is the motor specifications:
http://www.specamotor.com/en/Faulhaber/motors/2338-006S/datasheet_motor.html
i suppose to control the position in bi-direction.
the questions:
1-which power op-amp should i use?
2- is there a ready drive that i can buy ?
3-is this circuit correct to control the motor position in bi-direction?
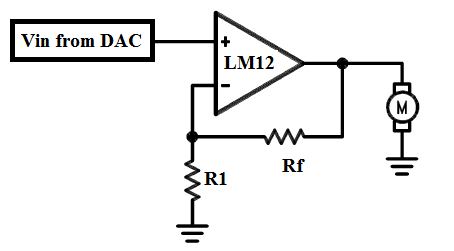
any help will be more than appreciated