i know these kind of sensors are sensitive but, man... how do they fail so easily ?!
My procedure:
- bake the MEMS sensors @ 125 deg C for 9 hours (dry out phase)
- apply solder paste over the boards through an electropolished stencil
- place the sensors by hand as straight as I can then put to oven for soldering as per
J-STD-020 - JEDEC. Not to a tee though; the cool down phase for instance is slower, I can not do -6 degC/s in my hobby oven.
- power the boards and test them in a fixture with a magnet; Same distances, same magnet, swipe direction, algorithm, positioning, etc
My success rate varies in the 30% - 70% interval. The failed chips will either not sense the magnet from the same distance or not sense it at all. Tried it with three sensors from three different producers.
I may also not respecting the general recommendations for soldering these chips to a tee, like the ones below, but really, is that why half my chips are failing ?
https://www.nxp.com/docs/en/application-note/AN3484.pdf
https://mcubemems.com/wp-content/up...andling-Assembly-Guideline-for-LGA-AN-001.pdf
https://www.st.com/resource/en/tech...rs--in-an-lga-package--stmicroelectronics.pdf
Thank you!
My procedure:
- bake the MEMS sensors @ 125 deg C for 9 hours (dry out phase)
- apply solder paste over the boards through an electropolished stencil
- place the sensors by hand as straight as I can then put to oven for soldering as per
J-STD-020 - JEDEC. Not to a tee though; the cool down phase for instance is slower, I can not do -6 degC/s in my hobby oven.
- power the boards and test them in a fixture with a magnet; Same distances, same magnet, swipe direction, algorithm, positioning, etc
My success rate varies in the 30% - 70% interval. The failed chips will either not sense the magnet from the same distance or not sense it at all. Tried it with three sensors from three different producers.
I may also not respecting the general recommendations for soldering these chips to a tee, like the ones below, but really, is that why half my chips are failing ?
https://www.nxp.com/docs/en/application-note/AN3484.pdf
https://mcubemems.com/wp-content/up...andling-Assembly-Guideline-for-LGA-AN-001.pdf
https://www.st.com/resource/en/tech...rs--in-an-lga-package--stmicroelectronics.pdf
Thank you!
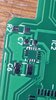
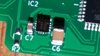