At the hackerspace I frequent we have a couple of laser cutters. We want to keep track of the laser time to track tube life.
Someone got inside and found a signal that is about 4V when the laser is off, and 0V when it's on. Some more investigation revealed that it can't sink or source much current at all.
The hour meter requires 12V to 80V and we have 24V available in the laser cutter, sharing the same ground with this signal.
The laser is controlled with PWM, and I don't know if this signal has that PWM on it or not, and we decided that we wanted to count laser time when engraving as the total time rather than the laser time (during engraving the laser turns on and off lots, and typically very quickly)
We drew up a few circuits, but I prefer what is essentially a pulse extender. The final circuit was this:
edit: this is updated in a post below.
I created a 5V rail from the 25V rail. The 4V input will appear as a logic HIGH to the Schmitt trigger inverters. There's a weak pull-up as well, and an input resistor to limit the current should the input voltage exceed the supply rails.
The input is inverted and extended. finally driving the gate of a mosfet. Whilst the mosfet isn't a logic level device, with 5V on the gate it can safely pass far more current than we need (which is a few mA for the hour meter).
Most of the complexity is for the various LED indicators, several of them being driven from spare inverters because there are 6 available, and I wasn't using all of them.
With the values shown, the pulse is extended by about half a second.
The whole prototype fits on a board about 5cm x 5cm with plenty of room around the outside for mounting holes and a terminal block.
Someone got inside and found a signal that is about 4V when the laser is off, and 0V when it's on. Some more investigation revealed that it can't sink or source much current at all.
The hour meter requires 12V to 80V and we have 24V available in the laser cutter, sharing the same ground with this signal.
The laser is controlled with PWM, and I don't know if this signal has that PWM on it or not, and we decided that we wanted to count laser time when engraving as the total time rather than the laser time (during engraving the laser turns on and off lots, and typically very quickly)
We drew up a few circuits, but I prefer what is essentially a pulse extender. The final circuit was this:
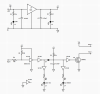
I created a 5V rail from the 25V rail. The 4V input will appear as a logic HIGH to the Schmitt trigger inverters. There's a weak pull-up as well, and an input resistor to limit the current should the input voltage exceed the supply rails.
The input is inverted and extended. finally driving the gate of a mosfet. Whilst the mosfet isn't a logic level device, with 5V on the gate it can safely pass far more current than we need (which is a few mA for the hour meter).
Most of the complexity is for the various LED indicators, several of them being driven from spare inverters because there are 6 available, and I wasn't using all of them.
With the values shown, the pulse is extended by about half a second.
The whole prototype fits on a board about 5cm x 5cm with plenty of room around the outside for mounting holes and a terminal block.
Last edited: