Hey all I am in need of some help with hooking up this little motor to the TB6612FNG Stepper Motor Drive Controller that I purchased. I am wanting some feedback on how to go about hooking it up to this deadbolt motor so that I dont mess up the motor. This board will be controlled by an Arduino.
The deadbolt insides look like this:
And the TB6612FNG is this:
Back of the board
Each pin and its function is covered in the table below.
Now, for a quick overview of how to control each of the channels. If you are using an Arduino, don’t worry about this too much as the library takes care of all of this for you. If you are using a different control platform, pay attention. When the outputs are set to High/Low your motor will run. When they are set to Low/High the motor will run in the opposite direction. In both cases, the speed is controlled by the PWM input.
Don’t forget STBY must be high for the motors to drive.
And the data sheet on the TB6612FNG is http://www.sparkfun.com/datasheets/Robotics/TB6612FNG.pdf.
I found a great tutorial http://bildr.org/2012/04/tb6612fng-arduino/ but want to make sure I hook up the wires correctly for this deadbolt motor and thats why I ask someone whos more knowledgeable about these types of things to help me out.
Thanks!
The deadbolt insides look like this:
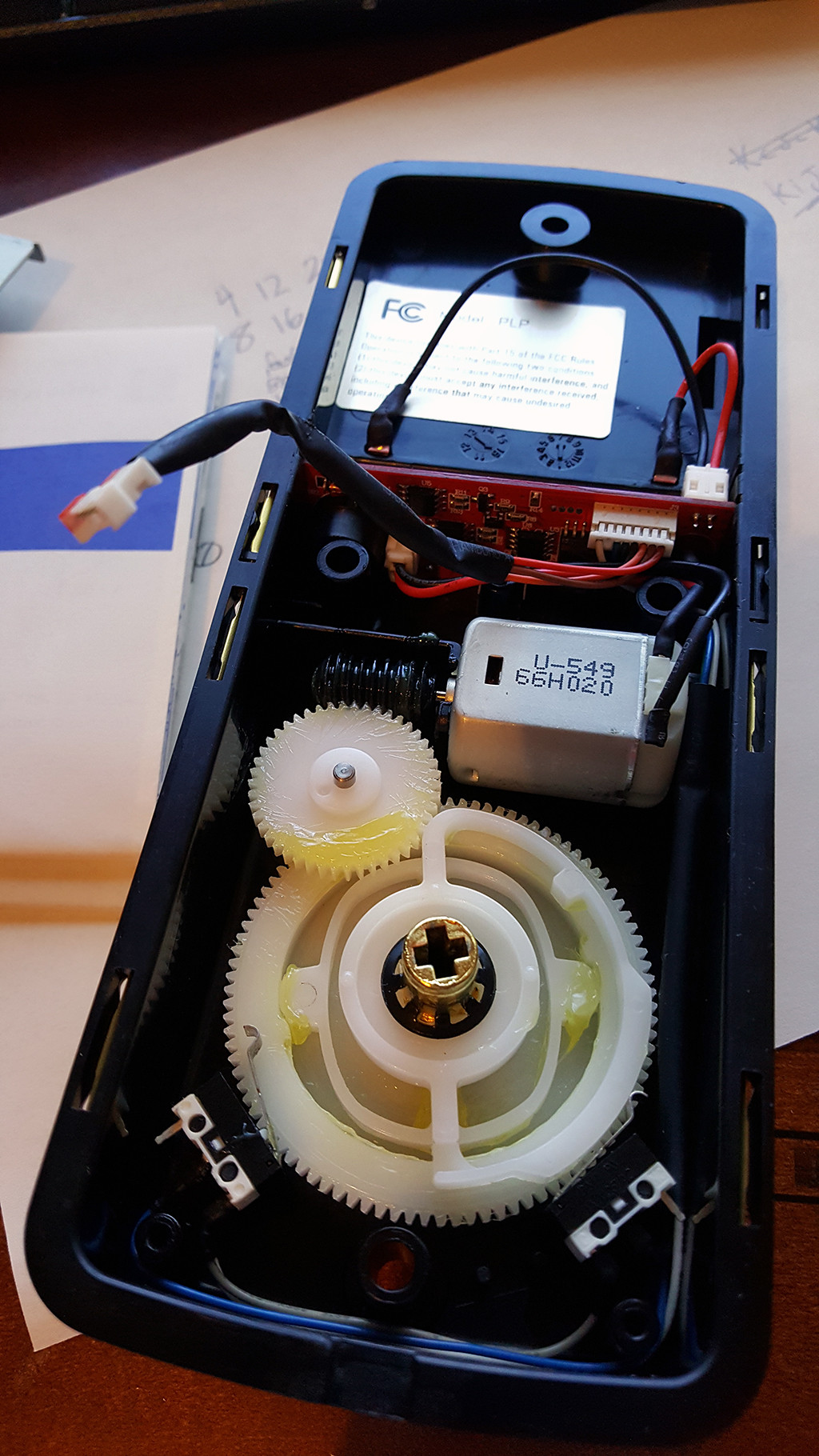
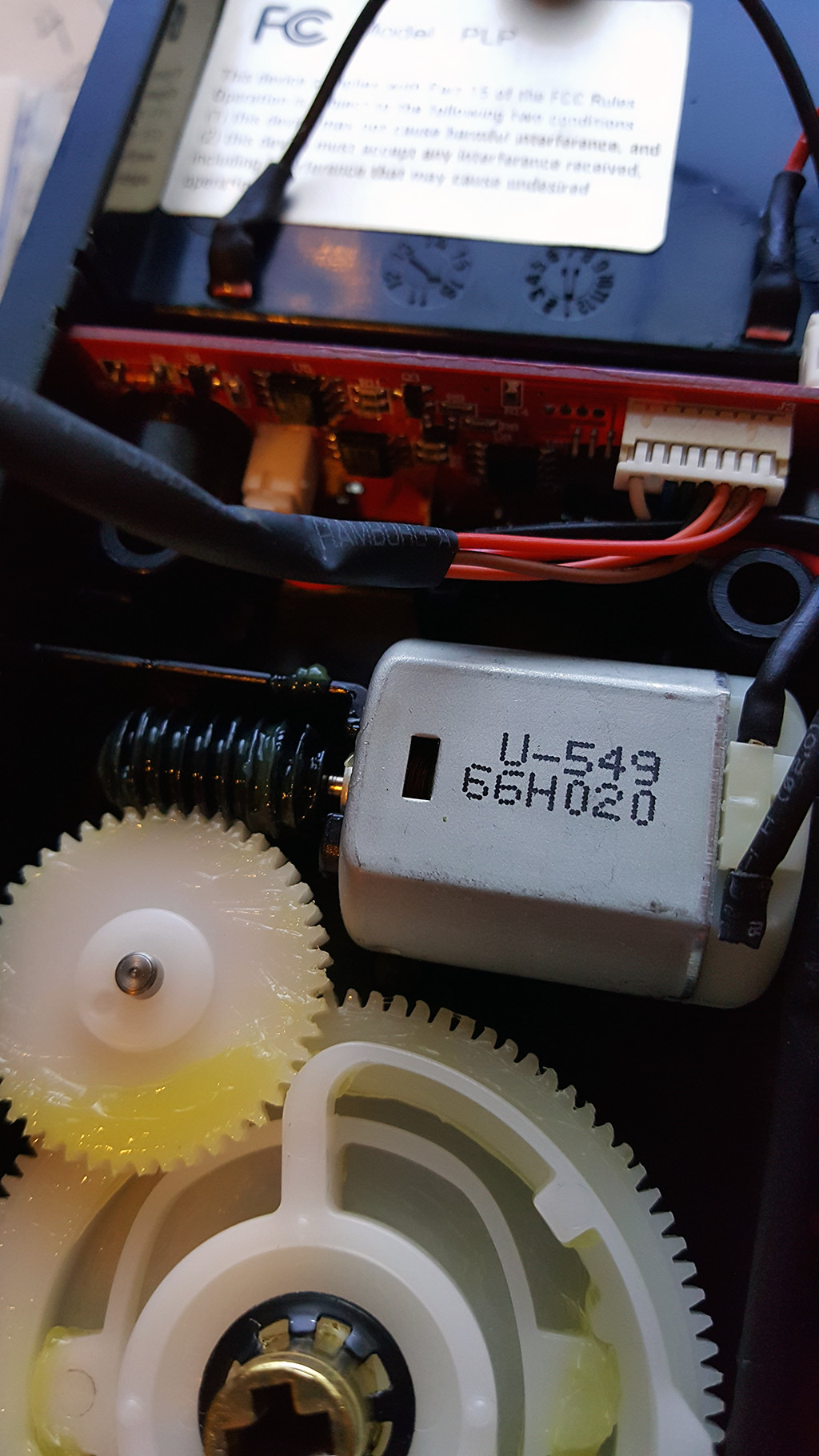
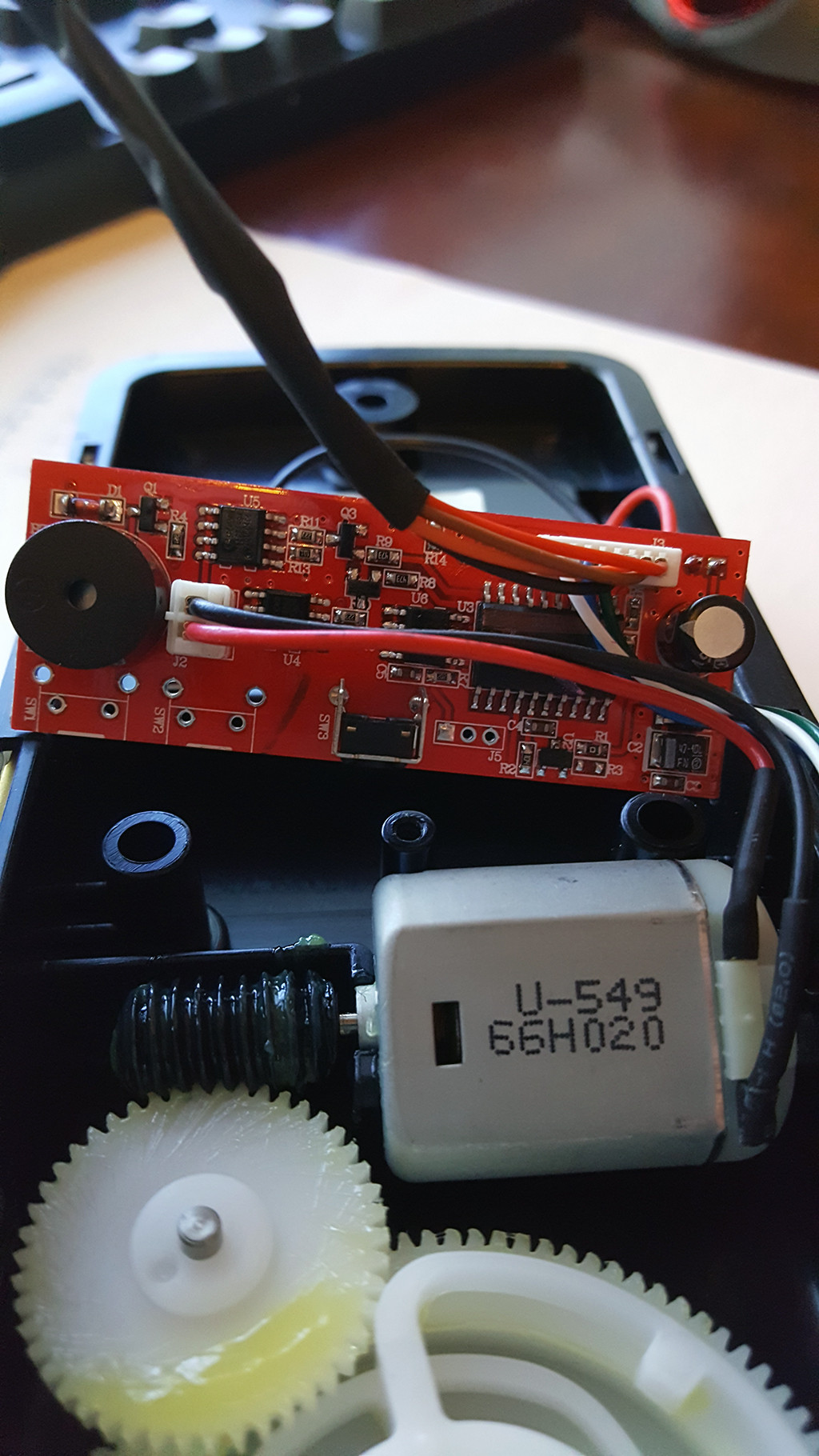
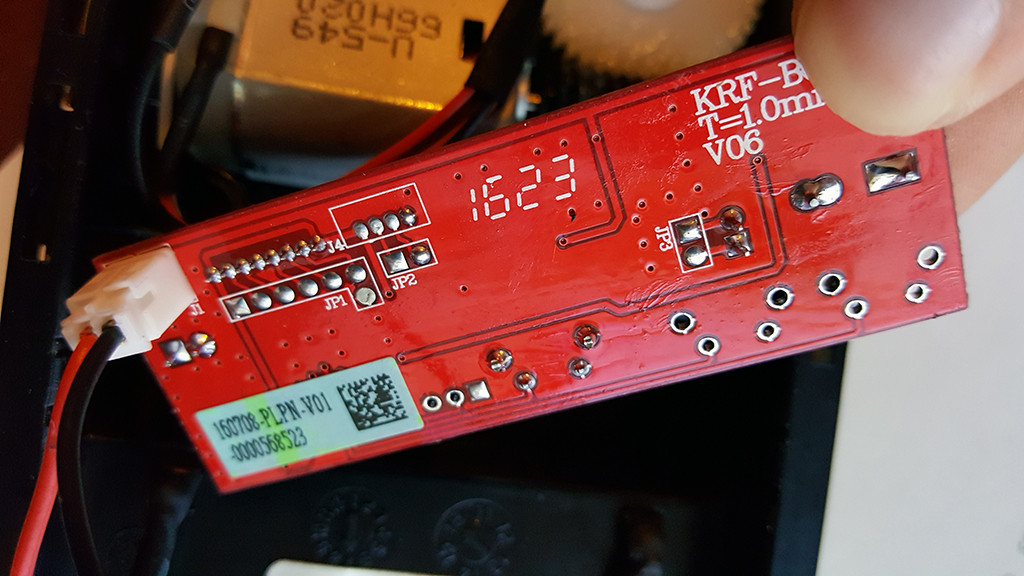
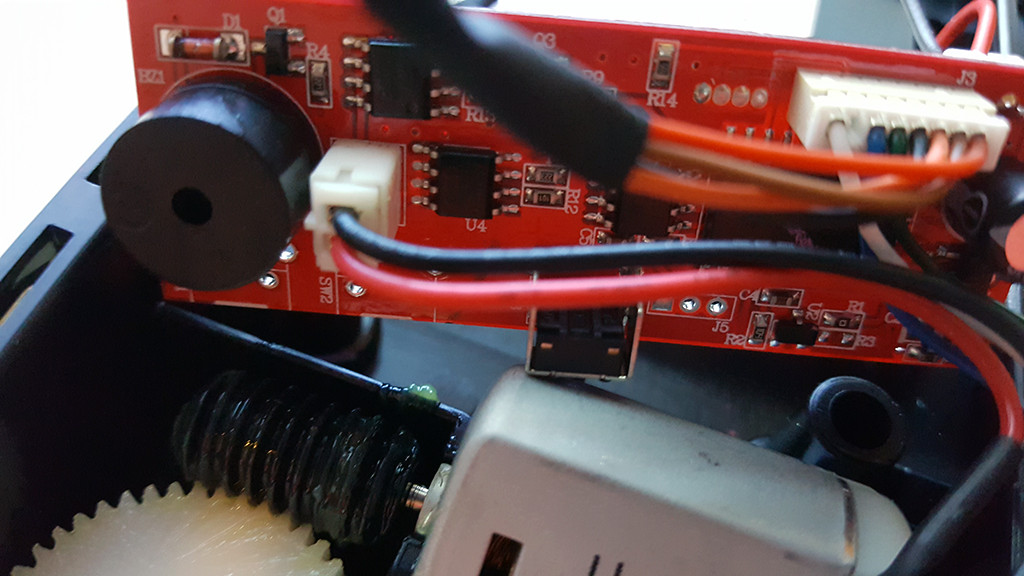
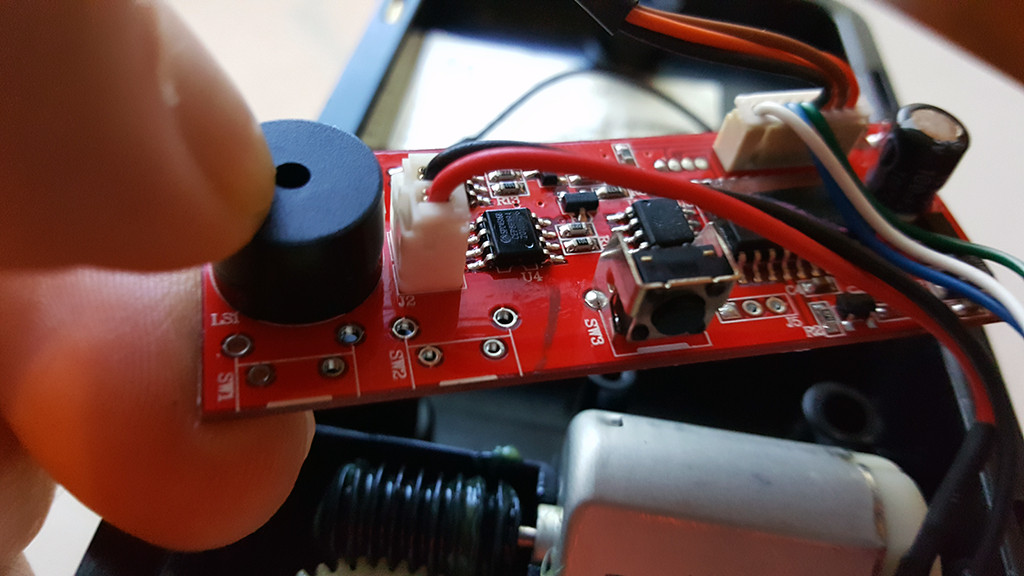
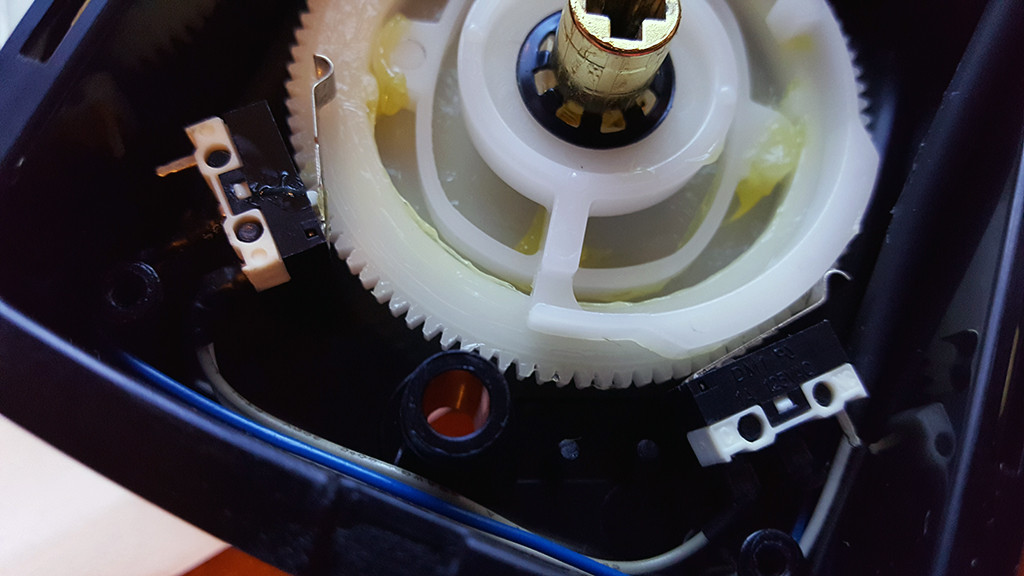
And the TB6612FNG is this:
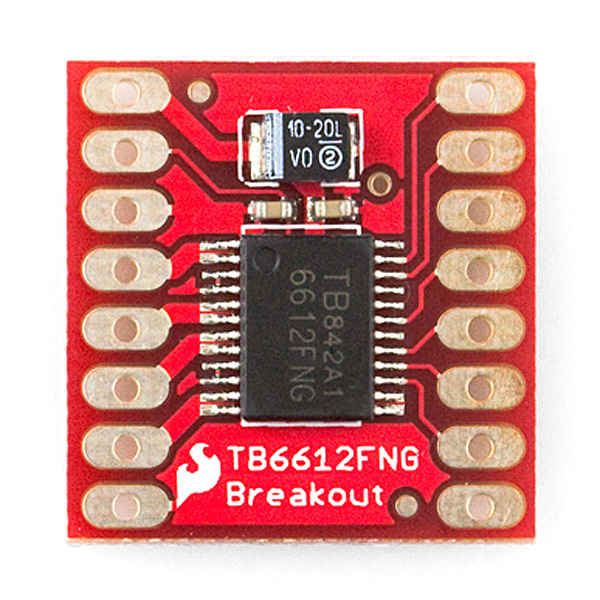
Back of the board
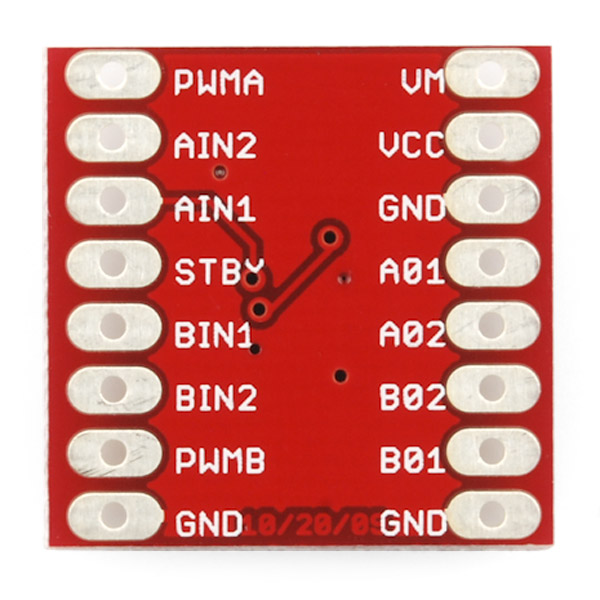
Each pin and its function is covered in the table below.
Code:
Pin Label Function Power/Input/Output Notes
VM Motor Voltage Power This is where you provide power for the motors (2.2V to 13.5V)
VCC Logic Voltage Power This is the voltage to power the chip and talk to the microcontroller (2.7V to 5.5V)
GND Ground Power Common Ground for both motor voltage and logic voltage (all GND pins are connected)
STBY Standby Input Allows the H-bridges to work when high (has a pulldown resistor so it must actively pulled high)
AIN1/BIN1 Input 1 for channels A/B Input One of the two inputs that determines the direction.
AIN2/BIN2 Input 2 for channels A/B Input One of the two inputs that determines the direction.
PWMA/PWMB PWM input for channels A/B Input PWM input that controls the speed
A01/B01 Output 1 for channels A/B Output One of the two outputs to connect the motor
A02/B02 Output 2 for channels A/B Output One of the two outputs to connect the motor
Code:
In1 In2 PWM Out1 Out2 Mode
H H H/L L L Short brake
L H H L H CCW
L H L L L Short brake
H L H H L CW
H L L L L Short brake
L L H OFF OFF Stop
And the data sheet on the TB6612FNG is http://www.sparkfun.com/datasheets/Robotics/TB6612FNG.pdf.
I found a great tutorial http://bildr.org/2012/04/tb6612fng-arduino/ but want to make sure I hook up the wires correctly for this deadbolt motor and thats why I ask someone whos more knowledgeable about these types of things to help me out.
Thanks!