I put somthing together for you. I will look at you design in due course. Hope it's of some use.
Cheers
Adam
Transmission Lines
What is a transmission line? Well it’s basically any pair on conductors used to guide electromagnetic energy from one point to another. In a PCB the transmission line is the trace above a power plane. This provides closely coupled send and return signal paths, with the return signal being directly underneath the send trace. This reduces loop inductance due to magnetic field cancelation.
Other types of transmission lines
· Twisted pair Cables
· RF Coaxial cable
· Waveguides
· Power traces
What’s happening on this transmission line?
Sometimes it’s advantageous to think of a mechanical transmission line, the simplest I can think of is what we call a newton’s cradle. The transmission line in this case is an acoustic version and Kinetic energy from one ball to the other propagates through the other balls at the speed of sound.
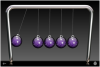
Figure 1 Newton’s Cradle Mechanical Transmission line
The middle balls don’t move they just compress and expand back again once they have transferred the energy to the other balls. Initially the last ball will swing up as high as the first ball that was released in the first place. In an Ideal world this would carry on for ever, the first and last balls alternatively swinging out as the cycle repeats itself.
Losses in the transmission line prevent this carrying on and eventually this dies out and stops. This is essential the same principle of what happens to an un-terminated PCB transmission line. Energy is reflected back and forth within the PCB trace causing corruption of the original signal. The way to prevent this is to somehow absorb this reflected energy.
Figure 2 Various PCB Transmission Lines Setups
Two common methods of termination that are used are series termination and parallel. Series termination is when the reflected wave is allowed to come back to the source and energy would be absorbed in a series resistor. Parallel termination is a method of using a shunt resistor at the load end which absorbs the reflected energy there and prevents this reflected energy from continuing back up the transmission line to the source.
Tip!
· If the insulating material between the transmission line has a dielectric constant that is constant with frequency then the impedance will be the same at all frequencies.
· If the cross sectional area of the transmission line is constant it will have the same impedance irrespective of length.
This is another good reason not to change layers on a transmission line because the via will contribute an impedance discontinuity and cause some reflection of the signal back to the source which reduces the amount energy transferred to the load which is used to develop the voltage signal at that end.
How do we control this?
If you are dealing with RF signals then there may be only a few lines that need controlled impedances which can be controlled quite easily. But on a high speed digital PCB this is much harder because trying to make sure all traces are matched is very time consuming. So a level of signal degradations needs to be accepted, this is down to the designer and product function. The most effective use of time for this approach is to use internal power planes.
Un-terminated
Figure 3
Figure 4 Response of un-terminated line
Series connection
Notice the reflections bringing back the losses from the potential divider formed by the different impedances.
Figure 5 Response of series terminated line
Parallel Termination
Noticed the lack of reflection, the output voltage is too small to trigger the 5 Volt logic level on the output. In this case the output impedance of the source must be a lot lower than the transmission line to achieve a logic 1 level on the output of the transmission line.
Figure 6 Response of parallel terminated line
Termination Techniques
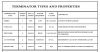
Figure 7 Different types of termination and their uses
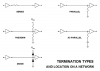
Figure 8 Termination configurations
Stubs on Transmission lines
Stubs on transmission lines can cause reflections which can cause the intended signal to interfere with itself. A stub can be intentional and is used for matching the impedance of very high speed transmission lines (microwave).
For the majority of high speed designs they cause a problem because they are uncontrolled and variable. How do you accidentally cause a stub problem? Two common mistakes I see quite often is when people change layers on a multilayer PCB which has through hole vias. And also the connecting of the terminating resistor which was fitted to help can actually cause problems.
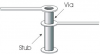
Figure 9 this is a via stub
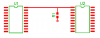
Figure 10 R1 has long Stub from signal trace, bad design
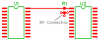
Figure 11 Better approach
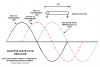
Figure 12 Quarter wave stub on transmission line. The stub shorts out the incoming signal by phase cancelation.
When do I need a transmission line or terminate an existing one?
Two general thoughts on this and one is when the quality and amplitude of the signal at the receiver end of a transmission line falls below design specifications. The other is when the length of the PCB trace exceeds the TEL (Total electrical length) of the signal.
Let’s put this into context.
A PCB trace will allow the propagation of a signal at approximately 6 inches per nanosecond. So if a trace is longer than 2.25 inches with signal rise times of 1.5 ns then this signal would need impedance control.
Decoupling Capacitors
Decoupling capacitors are used to provide a low impedance source of energy to high frequency high current switching that happens inside most ICs.
Capacitor Types
Aluminium Electrolytic: Large physical size, large capacitance values, High Voltage, Low ESR, degrade over time.
Tantalum: Medium physical size, Medium capacitance value, Low voltage, Low ESR.
Ceramic: Small Physical size, Low to medium values, Very low ESR.
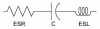
Figure 13 Equivalent capacitor circuit
ESR (Equivalent Series Resistance) Rs
Capacitance XC = 1/2πfC
ESL (Equivalent Series Inductance) XL = 2πfL
Series Resonance
Series resonance occurs at the frequency where XC (capacitive reactance) is equal to XL (inductive reactance). At this frequency, the impedance of the capacitor becomes equal to the ESR. At frequencies above this, the capacitor behaves like an inductor.
Parallel Resonance
The additional capacitance of the PCB and its power planes cause parallel capacitance which increases the resonant frequency of the capacitor. At this frequency the capacitor has much higher impedance.
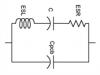
Figure 14 Parallel equivalent circuit
So it’s important to choose the correct value and type of capacitor for the design. For many years the standard decoupling capacitor has been 100nF. This is the value I use today for low frequency PCBs. For higher frequencies you need to go lower.
Some people say you can use the capacitance of the power planes. Although this is true, it is quite low value doesn’t make a very good capacitor. The best approach is to choose a ceramic capacitor which has the correct value. Bulk capacitance somewhere in the region of 1uF to 10uF would be used to support the supply pin of a microprocessor.
Capacitor example:
IC power consumption = 1 W
Power Supply =3.3 Volts
Decoupling capacitor = 1nF
Support Time for 5% Droop of supply = C*0.05*V^2/P = 0.5 ns
Another method:
dt=rise time
dv=drop in voltage allowed
C=Total I/O current *dt/dv = 100 mA*1 ns/10 mV= 10 nF
Now this small value will work for very short pulses of energy like the switching of internal ports in ICs. But will do nothing to support the power supply from dipping due to loading on the PCB from other parts of the circuitry or small power dips from the input to the power supply. This is why you need some bulk capacitance from larger value capacitors.