Hi ALL!! I'm new here.
I'm trying to create a conversion for my Lincoln AC-225 arc welder, to add DC welding capability (as opposed to paying an extra $400 for a production unit).
Here's what I have so far, with the addition of a properly sized bridge rectifier, I can successfully convert the AC waveform to DC. But, the waveform is not steady like I need it to be (as seen on the right of the following image)...
For DC welding, the DC current needs to be as smooth as possible, otherwise the welder has to deal with constant arc instability (thus, a crappy weld no matter how great at welding the guy making the weld is).
I have read a lot about adding a capacitor to the output to "smooth" the current to a "ripple" (shown in the next image), but due to the voltage and amperage involved, an inductor might be a better choice. Please post your opinion if you disagree.
So here's my dilemma, I can't seem to be able to find any info (that I can understand) that would help me size the inductor coil to this application.
Here's the current specs:
48-53V @ 30-225A
The voltage is almost a constant.
The amperage is selectable on the AC side of the rectifier via a knob on the front of the welder. Available max amperage can be selected from 30A to 225A. While welding at whatever amperage is selected, the actual amperage can vary depending on many factors, but not to exceed the max amperage selected via the amperage selection knob.
So that's about it.
I could use your help to finish this project.
I'm trying to create a conversion for my Lincoln AC-225 arc welder, to add DC welding capability (as opposed to paying an extra $400 for a production unit).
Here's what I have so far, with the addition of a properly sized bridge rectifier, I can successfully convert the AC waveform to DC. But, the waveform is not steady like I need it to be (as seen on the right of the following image)...
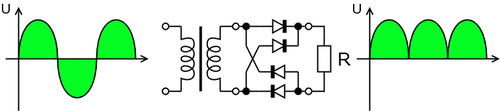
For DC welding, the DC current needs to be as smooth as possible, otherwise the welder has to deal with constant arc instability (thus, a crappy weld no matter how great at welding the guy making the weld is).
I have read a lot about adding a capacitor to the output to "smooth" the current to a "ripple" (shown in the next image), but due to the voltage and amperage involved, an inductor might be a better choice. Please post your opinion if you disagree.
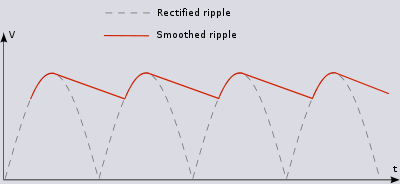
So here's my dilemma, I can't seem to be able to find any info (that I can understand) that would help me size the inductor coil to this application.
Here's the current specs:
48-53V @ 30-225A
The voltage is almost a constant.
The amperage is selectable on the AC side of the rectifier via a knob on the front of the welder. Available max amperage can be selected from 30A to 225A. While welding at whatever amperage is selected, the actual amperage can vary depending on many factors, but not to exceed the max amperage selected via the amperage selection knob.
So that's about it.
I could use your help to finish this project.