How do I connect and insulate wires in high temp environments? I'm talking about 600-700 F heat, so soldering and heat shrink are not possible.
I have this crimper:
https://www.amazon.com/gp/product/B0045CUMLQ/
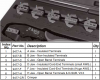
Often when I try to crimp open barrel connectors, I either get loose connections that come apart or the crimp is so tight that half of the wire strands get cut! Can someone give me some advice? Are there alternatives to crimping in high heat environments, like welding the wires together somehow? I was also considering brazing wires together with low melting point brazing rods, since I have a soldering iron that goes as high as 899F. I also have this butane torch:
https://www.amazon.com/gp/product/B000WOHSHM
Will that get hot enough?
And what's the best way of isolating the wires from each other and nearby metal chassis?
I have this crimper:
https://www.amazon.com/gp/product/B0045CUMLQ/
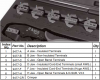
Often when I try to crimp open barrel connectors, I either get loose connections that come apart or the crimp is so tight that half of the wire strands get cut! Can someone give me some advice? Are there alternatives to crimping in high heat environments, like welding the wires together somehow? I was also considering brazing wires together with low melting point brazing rods, since I have a soldering iron that goes as high as 899F. I also have this butane torch:
https://www.amazon.com/gp/product/B000WOHSHM
Will that get hot enough?
And what's the best way of isolating the wires from each other and nearby metal chassis?
Last edited: