Hi
I am building a small CNC plotter using 2 DVD stepper motors for X and Y axis.
For driving the unit, I am using:
Main processor: Arduino Nano
H-Bridge driver: L293D
Software: BENBOX
For initial testing I wired Arduino Nano and L293Ds on breadboard as below:
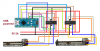
For external power I am using a 5V-2A cell phone charger with customized cable.
Now, the problem is that the motors are not responding to the calibration step provided in BENBOX.
Please let me know if the wiring is correct. Any idea where am I wrong. BTW, this is my first CNC project and I took help from this video for BENBOX and the firmware
I am building a small CNC plotter using 2 DVD stepper motors for X and Y axis.
For driving the unit, I am using:
Main processor: Arduino Nano
H-Bridge driver: L293D
Software: BENBOX
For initial testing I wired Arduino Nano and L293Ds on breadboard as below:
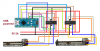
For external power I am using a 5V-2A cell phone charger with customized cable.
Now, the problem is that the motors are not responding to the calibration step provided in BENBOX.
Please let me know if the wiring is correct. Any idea where am I wrong. BTW, this is my first CNC project and I took help from this video for BENBOX and the firmware
Last edited: