I have invested in a battery bank to drive my LED night sensor spotlights. About $550 worth. I have 8 cells of 3.2V each in series to give 25.6 V nominal . They must be charged to no more than 3.55V and must not go below 2.5V . Thats the manufacturers recommendation and thats what i will stick to .
Now BMS systems are expensive . $400 and up to suit my pack.
So I found these cheap ebay boards advertised for 12V systems for $10 or so each and I thought I wonder if I can use two of these in series to monitor my bank whilst charging and discharging.
So I have them in front of me and have the pleasant task of trying to wire them up effectively.
Hmm so I'm stuck. I attach a scan of what I thought I could do but don't know how to treat the negative lines of unit one and unit two.
It seems logical to me that if i halve the pack and put a board on each there should be a way to series them and get 24Volt output . Clearly these devices work on the negative rail with a make and break circuit but I don't understand how . There are not any LEDs that light up as each cell reaches full either.
My charge system is by solar controller at 24Volts so I cant supply 12 Volts to each board separately without difficulty. Here is the ebay site for specs which are not quite what I want but will do to start me off .https://www.ebay.com.au/itm/4S-w-Balance-100A-3-2V-LiFePo4-LiFe-18650-Battery-Cell-PCB-BMS-Protection-Board/401520816753?ssPageName=STRK:MEBIDX:IT&_trksid=p2057872.m2749.l2649
Anybody able to help me out ?
Can I just hook the negatives together? C is charge input and P is Power out=load ,discharge

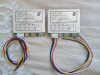
Now BMS systems are expensive . $400 and up to suit my pack.
So I found these cheap ebay boards advertised for 12V systems for $10 or so each and I thought I wonder if I can use two of these in series to monitor my bank whilst charging and discharging.
So I have them in front of me and have the pleasant task of trying to wire them up effectively.
Hmm so I'm stuck. I attach a scan of what I thought I could do but don't know how to treat the negative lines of unit one and unit two.
It seems logical to me that if i halve the pack and put a board on each there should be a way to series them and get 24Volt output . Clearly these devices work on the negative rail with a make and break circuit but I don't understand how . There are not any LEDs that light up as each cell reaches full either.
My charge system is by solar controller at 24Volts so I cant supply 12 Volts to each board separately without difficulty. Here is the ebay site for specs which are not quite what I want but will do to start me off .https://www.ebay.com.au/itm/4S-w-Balance-100A-3-2V-LiFePo4-LiFe-18650-Battery-Cell-PCB-BMS-Protection-Board/401520816753?ssPageName=STRK:MEBIDX:IT&_trksid=p2057872.m2749.l2649
Anybody able to help me out ?
Can I just hook the negatives together? C is charge input and P is Power out=load ,discharge

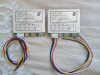
Last edited: